By Dr. Sadik Omairey, Founder of NmeX Non-metallic Engineers Exchange
Despite decades of success in select applications, the broader adoption of non-metallic piping systems remains hesitant in many major industries, particularly oil & gas and utilities. While the benefits are clear, lightweight systems, corrosion resistance, lower maintenance, non-metallic systems often face a barrier of confusion, limited awareness, and insufficient procedural development.
It’s worth noting that some organisations are already taking initiative. Saudi Aramco, for example, has developed a non-metallic strategy and updated several engineering standards to encourage, and in some cases mandate, the evaluation of RTR (Reinforced Thermosetting Resin) and RTP (Reinforced Thermoplastic Pipe) systems in applicable projects.
This article explores why such hesitation persists and what can be done to close the gap.
The Root Causes of Hesitation
- Lack of Awareness: Many engineering and design teams default to metallic systems simply because that is what they are trained on. Non-metallic piping systems are still viewed by some as “niche” or “alternative,” rather than core materials. There is limited structured training, education, or awareness of non-metallics, particularly RTR and RTP systems. This leads to their omission at early project stages and missed opportunities for innovation.
- Uncertainty in Process and Responsibilities: The introduction of non-metallics often raises a host of new technical and procedural questions. Design teams must determine which codes apply (e.g., ISO 14692, API 15S), who owns the specification and approval process, and what inspection regimes are appropriate. Unlike metallic systems, non-metallics lack reliable, standardized inspection methods for weld/joint integrity. This means traditional techniques like radiography or ultrasonic testing are not applicable, requiring a completely different mindset and approach.
- Underdeveloped Procedures and Supply Chain: The supply chain for metallic systems is mature: vendors are prequalified, QA/QC plans are standardised, and materials are readily available. In contrast, RTR and RTP systems often require project-specific procedures, vendor qualifications, and specialist QA/QC processes, including resin testing, stiffness evaluation, and joint system validation. Compounding this is a shortage of skilled jointing personnel, and the lack of a widely accepted, international training and certification programme for non-metallic jointers remains a major barrier.
- CAPEX vs. OPEX Mindset: Another hesitation lies in the economic evaluation. Non-metallics often appear less competitive on a CAPEX basis when compared to carbon steel. However, the true benefit, in terms of corrosion resistance, reduced maintenance, and extended service life, only emerges in the OPEX phase. This delayed value proposition is often difficult to quantify upfront, particularly in rigid procurement environments focused on lowest initial cost.
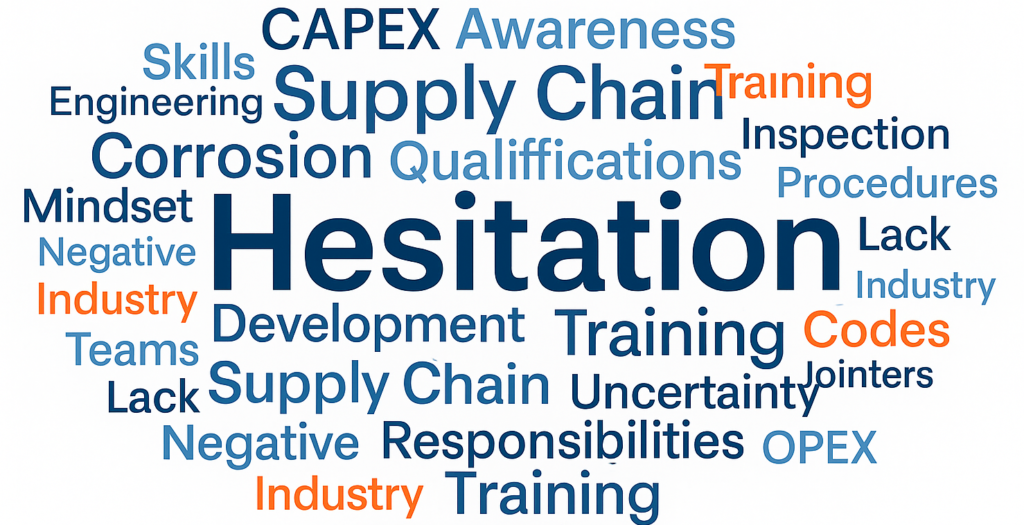
Comparison Across the Project Lifecycle
The table below illustrates how responsibilities, expectations, and complexity differ between metallic and non-metallic piping systems throughout a project lifecycle:
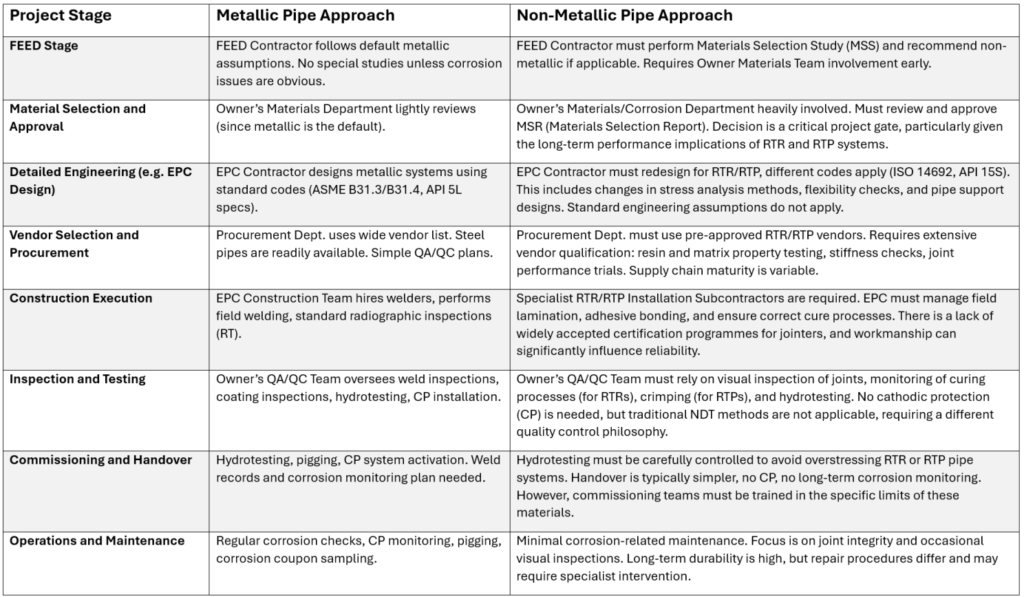
Bridging the Gap
To accelerate non-metallic adoption where suitable, we must:
- Raise awareness at the FEED and material selection stages: By the time a project reaches EPC, most decisions are locked in. Early-stage awareness, particularly within FEED contractors and owners’ materials teams, is crucial to ensure non-metallic options are seriously considered.
- Clarify applicable codes, design criteria, and approval workflows: Many engineers are unfamiliar with the relevant standards (e.g. ISO 14692 for RTR, API 15S for RTP). Clear guidance on which codes apply and who is responsible for what can eliminate delays and design missteps.
- Invest in non-metallic-specific construction practices and training: The lack of widely accepted training and certification for RTR/RTP jointers is a serious industry gap. Establishing global benchmarks for jointer competency is essential to building confidence.
- Support vendors and operators in developing consistent QA/QC and installation practices: Standardised QA/QC procedures for adhesive bonding, lamination curing, and joint testing are essential. Until then, each project must reinvent its own processes, increasing risk and cost.
- Educate decision-makers on total lifecycle cost, not just CAPEX: The benefits of non-metallics accrue over time through reduced maintenance, no corrosion-related failures, and longer service life. Framing value in terms of total cost of ownership, not initial material price, will unlock more balanced evaluations.
With these changes, non-metallic systems can shift from being seen as risky and unfamiliar, to being viewed as robust, optimised solutions for modern pipeline challenges.
At NmeX Non-metallic Engineers Exchange, this is one of our core focus areas. If you have insights to share, please let us know [email protected] or www.nonmetallic.co.uk