By Dr. Sadik Omairey, Founder of NmeX Non-metallic Engineers Exchange
Capital expenditure (Capex) has traditionally been the dominant metric in material selection decisions across engineering and infrastructure sectors. However, this approach often overlooks the long-term implications of operational expenditure (Opex), a gap that becomes especially evident when comparing metallic and non-metallic materials.
This article examines four decades of material price trends (1980–2024), highlighting the evolving cost-effectiveness of non-metallics and the need to integrate lifecycle thinking into engineering decision-making.
Real-World Evidence
While theoretical models and lab performance metrics are useful, the strongest argument for non-metallic adoption lies in real-world data. Over the past two decades, several operators and suppliers have documented clear lifecycle and cost advantages when deploying composite and thermoplastic pipe systems, particularly in demanding sectors such as oil and gas, infrastructure, and remote field development.
From reduced installation time to the elimination of corrosion mitigation systems, and from lighter logistics to proven carbon savings, the following examples demonstrate how non-metallic solutions are delivering both economic and environmental returns:
Baker Hughes’ on‑shore composite flexible pipe is reported to reduce installed costs by over 20% compared to steel. The spoolable design simplifies logistics and installation, eliminating heavy pipe joining, reducing onsite equipment needs, and allowing land‑right‑of‑way reductions.
According to Mattr, their Flexpipe products are designed for 20 years of service with reliable performance, and are promoted as requiring no large-scale chemical inhibitor programs or expensive maintenance routines. On their website, Mattr states that Flexpipe systems have helped customers achieve 30–40% capital cost savings and 50% reduction in installation crew size compared to steel.
Strohm has posted the operational benefits of TCP, particularly its immunity to corrosion. According to their published insights, corrosion accounts for approximately 50% of oil pipeline spills globally, often requiring continuous injection of corrosion inhibitors and frequent pigging operations, both of which raise operational costs and reduce uptime. In contrast, TCP eliminates these issues entirely, reducing total operating expenditure and infrastructure complexity. Notably, operators working with TCP have been able to downscale field architecture—eliminating inhibitor tanks and pumps, lowering power demands, and enabling lighter, solar-powered platforms. This shift not only reduces capex and opex, but also enhances environmental and safety performance, making TCP an attractive long-term solution in offshore and remote settings.
On the other hand, a Life Cycle Assessment by Zubail et al. compared non-metallic composite pipes with carbon steel for onshore oil and gas flowlines. The study found that non-metallic pipes can reduce CO₂ emissions by up to 60% and energy use by up to 50% compared to steel, largely due to lower manufacturing emissions and reduced material mass. These findings support the environmental advantage of composite pipes, particularly when corrosion resistance and long service life are critical.
These are just a few examples of how non-metallic technologies are reshaping cost, sustainability, and reliability benchmarks in pipeline systems. As more operators document real-world benefits across performance, installation efficiency, and lifecycle impact, the case for accelerated adoption continues to grow.
Material Price Evolution: 1980 to 2024
Using compiled historical data, we have visualised the average international price per kilogram for common engineering materials, including steel, carbon fibre, glass fibre, epoxy resin, vinyl ester, and several thermoplastics (HDPE, PVDF, PA, ABS).
Non-metallic materials have demonstrated significant long-term price reductions.
Carbon fibre, for example, has seen a price drop of over 90% since the 1980s.
Glass fibre, epoxy, and thermoplastics also show downward trends, a result of improvements in manufacturing, scalability, and global adoption.
In contrast, steel prices have remained relatively stable over the same period, with periodic spikes due to geopolitical or market-driven disruptions.
The following video illustrates these trends dynamically, showing the relative change in material prices over time:
Operational Cost Considerations
While capital cost is often the focus during procurement, operational cost is the defining factor in the total lifecycle cost of an asset. This is where non-metallic materials consistently outperform their metallic counterparts.
1. Maintenance-Free Operation
Non-metallics such as glass fibre composites, carbon fibre reinforced polymers, and thermoplastic systems are inherently resistant to corrosion, oxidation, and moisture ingress. Unlike steel or other metals, they do not require:
- Cathodic protection
- Coating or painting systems
- Regular inspection regimes for corrosion monitoring
- Periodic recoating, gritting, or patch repair
This results in dramatically lower ongoing maintenance costs, both in direct spending and in indirect expenses associated with downtime and labour.
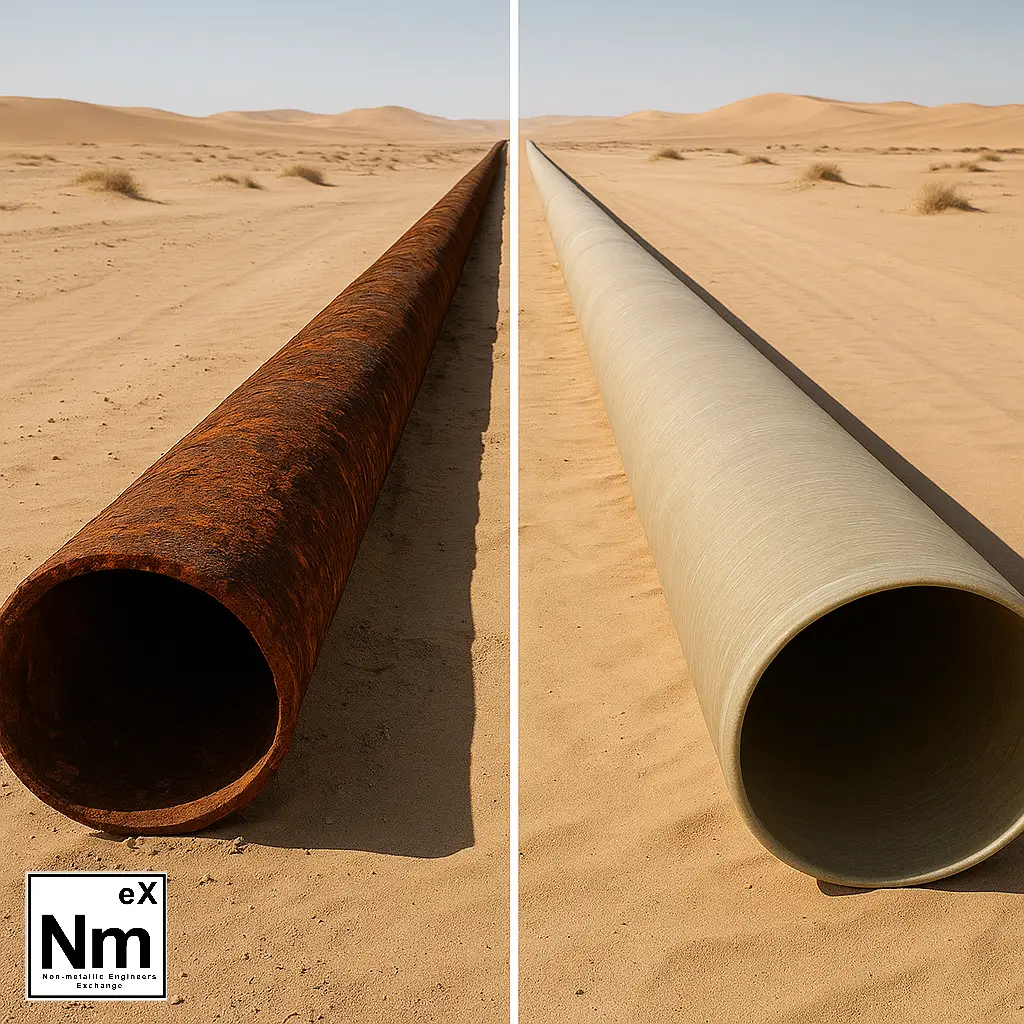
2. Less Shutdowns or Production Interruptions
In industrial environments, especially in oil & gas, chemical processing, and utilities, metallic components may require shutdowns for inspection (e.g., internal corrosion checks), repairs (e.g., weld or flange integrity), or replacements due to wall thinning or pitting. These interruptions carry high opportunity costs.
Non-metallics, by contrast, allow for continuous operation. If designed, manufactured, and operated properly, performance does not degrade significantly over time under most in-service conditions, and they are often immune to the failure modes that affect metals in aggressive environments.
3. Faster Deployment and Reduced Installation Time
One of the less appreciated but highly impactful benefits of non-metallic systems, especially flexible composite pipes (FCPs), is the significant reduction in installation time. Unlike traditional metallic pipelines that often require welding, surface treatments, cathodic protection, and joint-by-joint assembly, FCPs are spoolable, joint-free over long lengths, and can be deployed using compact reel-based systems.
This streamlined deployment process not only minimizes downtime and labor costs but is also invaluable in remote or challenging environments where logistics and skilled labor availability are constraints. In emergency or temporary scenarios, the ability to lay down kilometers of piping within hours rather than days is a major operational advantage.
4. Lightweight Structure and Lower Carbon Footprint
Non-metallic materials are intrinsically lighter than their metallic counterparts. This translates into multiple benefits across the lifecycle, from manufacturing to transportation and installation. Lower weight means:
- Reduced transportation energy consumption, especially for landlocked or offshore projects.
- Smaller and fewer lifting assets required on-site, improving safety and lowering fuel and equipment emissions.
- Less structural support decreasing civil works and project footprint.
Moreover, the lower embodied energy of many non-metallics compared to metals, combined with their long service life and minimal maintenance, contributes significantly to reducing overall carbon emissions. This aligns closely with decarbonization and ESG (Environmental, Social, Governance) goals, making non-metallics not only a functional upgrade but a responsible one.
5. Ideal for Difficult Access Zones
In infrastructure such as:
- Offshore platforms
- Buried pipelines
- Subsea manifolds
- Remote transmission stations
Maintenance access is logistically complex and costly. Every maintenance operation may involve divers, lifting equipment, confined space permits, or specialist crews. Using maintenance-free materials in these zones directly reduces total cost of ownership and enhances uptime.
Resilience Against Geopolitical Risk
A notable observation from the long-term dataset is the volatility of metallic material prices in response to geopolitical or economic shifts. Steel and other metals are subject to global market pressures and supply chain vulnerabilities. In contrast, many non-metallics can be produced locally, particularly in regions with growing polymer and composite manufacturing capacity.
For example, the Middle East has the potential to establish local non-metallic value chains that reduce dependence on imported metallics and enhance supply resilience. For instance, polymers needed can be manufactured by aramco ‘s SABIC in KSA and ADNOC Group‘s Borouge in the case of UAE.
The figure below shows how interconnected all of the stakeholders of non-meatllics are, which presents an excellent opportunity for complete circularity:
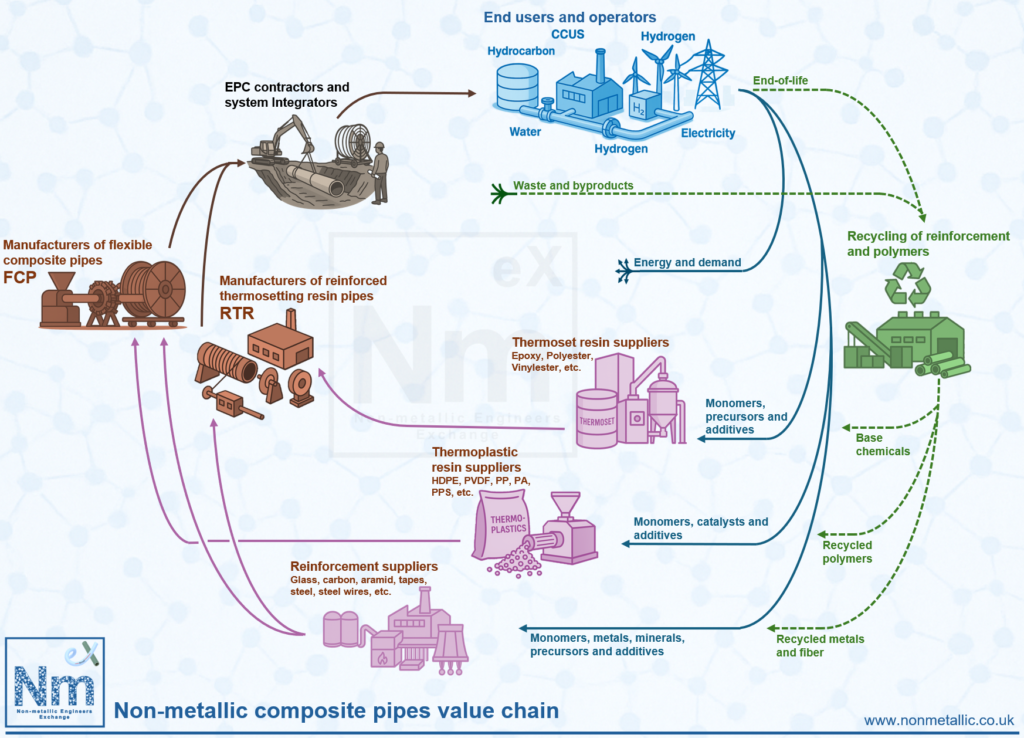
Conclusion: Engineering for Lifecycle Value, Not Just Procurement Cost
The long-term economic and operational advantages of non-metallic materials are becoming increasingly evident across multiple sectors. With significant price reductions over the past four decades, combined with their corrosion resistance, minimal maintenance needs, faster deployment, and lower carbon footprint, non-metallics now present a technically and commercially robust alternative to traditional metallic systems.
Decision-makers must move beyond Capex-only thinking. Total cost of ownership, operational resilience, and sustainability performance should drive material selection, especially in sectors where asset longevity, uptime, and regulatory compliance are paramount.
Non-metallics are no longer a niche innovation, they are a strategic enabler of reliable, low-carbon infrastructure.